Важнейшим условием содержания автосцепного устройства вагонов и локомотивов в исправности является своевременное обнаружение дефектов и их устранение. Основное внимание должно быть обращено на осмотр и ремонт автосцепного устройства перед включением вагонов в поезд и перед выходом локомотива под поезд.
Для осмотра автосцепного устройства вагонов используется время стоянки их в парках прибытия, формирования и отправления на сортировочных станциях, в пунктах массовой погрузки и выгрузки, при текущем ремонте. Автосцепное устройство локомотивов, а также электросекций осматривается и ремонтируется во время нахождения их в основном или оборотном депо.
Осмотр и проверка состояния автосцепного устройства вагонов производятся:
- у отдельно стоящих вагонов, подготовляемых к включению в поезда, когда автосцепки находятся в несцепленном состоянии;
- в поездах на пунктах технического осмотра, когда автосцепки сцеплены.
Во всех случаях производится тщательный наружный осмотр для выявления трещин, изломов и других повреждений автосцепного устройства, угрожающих безопасности движения поездов, и проверяется надёжность крепления деталей.
У каждой автосцепки отдельно стоящих вагонов проверяются величина износов замка и зубьев корпуса, ширина зева, а также действие механизма, для чего удобно пользоваться комбинированным шаблоном Холодова (фиг. 108).
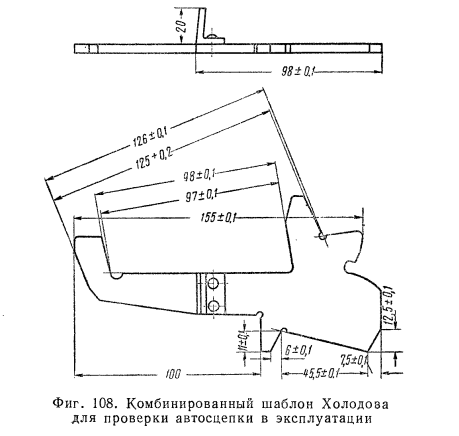
Для проверки действия предохранителя замка от саморасцепов шаблон прикладывается уголком к тяговой стороне и носку большого зуба так, чтобы конец шаблона нажимал на лапу замкодержателя, как показано на фиг. 109. Сохраняя такое положение шаблона, нужно несколько раз попробовать втолкнуть рукой замок внутрь головы автосцепки. Предохранительное устройство от саморасцепа считается исправным, если замок не уходит дальше упора верхнего плеча ссбачки в противовес замкодержателя.
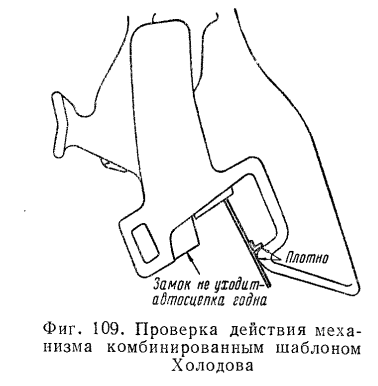
При такой проверке создаются наиболее невыгодные, возможные в эксплуатации условия работы предохранительного устройства. При расстоянии 98 мм от угольника шаблона до его кромки, нажимающей на лапу замкодержателя, обеспечивается такое положение противовеса, какое он занимает при растянутом состоянии автосцепок, имеющих предельный допускаемый в эксплуатации износ зубьев.
Далее проверяется устойчивость замка автосцепки в расцепленном положении до разведения вагонов. В исправном механизме замок, уведённый поворотом расцепного рычага из зева в карман головы автосцепки, должен удерживаться’в таком положении после возвращения рукоятки расцепного рычага в нормальное вертикальное положение. Замок должен опуститься в первоначальное положение после разведения расцепленных вагонов, когда прекратится нажатие малым зубом смежной автосцепки на лапу замкодержателя.
Для проверки этого у отдельного вагона нужно создать положение деталей механизма автосцепки, аналогичное тому, какое они занимают в поезде или в группе вагонов после поворота расцепного рычага. Шаблон нужно приложить, как и при предыдущей проверке (см. фиг. 110), а затем рукой повернуть валик подъёмника автосцепки до отказа в сторону буферного бруса и тотчас отпустить его, сохраняя прежнее положение шаблона.
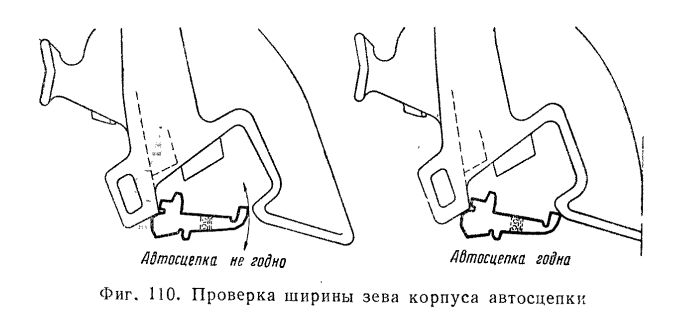
При исправном механизме замок будет оставаться в верхнем положении, пока шаблон не будет убран, и опустится в нижнее положение под действием своего веса после прекращения нажатия шаблоном на лапу замкодержателя. Для проверки ширины зева корпуса автосцепки замок уводится в карман, а шаблон одним концом прикладывается к углу малого зуба, как показано на фиг. НО, а другим подводится к носку большого зуба. Если этот конец шаблона не проходит в зев, то автосцепка считается годной. Эта проверка производится на среднем участке по высоте малого зуба, считая по 80 мм вверх и вниз от продольной оси автосцепки.
Толщина выступающей в зев части замка проверяется шаблоном, как показано на фиг. 111. Если шаблон прилегает к стенке малого зуба и одновременно своим выступом касается рабочей боковой поверхности замка или между последними остаётся зазор, то замок негоден и подлежит замене.
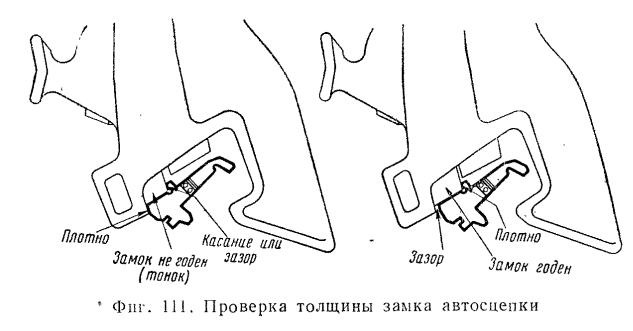
Износ тяговой стороны большого зуба и ударной стенки зева автосцепки проверяется установкой шаблона, как показано нафиг. 112. Если шаблон проходит между проверяемыми поверхностями, то автосцепка не годна и направляется в ремонт, а на вагон устанавливается другая. Эта проверка производится в средней части большого зуба, считая по 80 мм автосцепки, за исключением участка против окна для лапы замкодержателя.
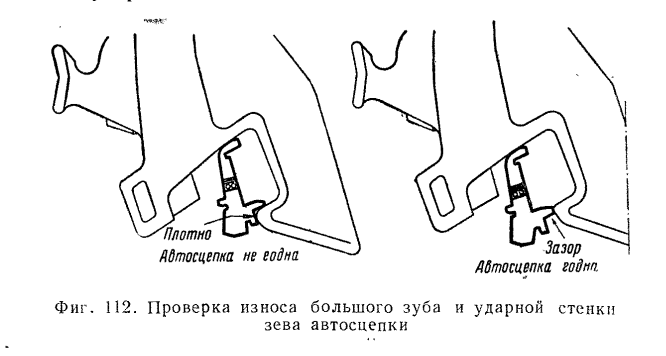
Проверка изношенности малого зуба производится шаблоном, как показано на фиг. 113. Если шаблон продвигается по тяговой и ударной сторонам малого зуба так, что внутренняя кромка выреза касается боковой стенки последнего, то автосцепка не годна и также подлежит замене и отправке в ремонт.
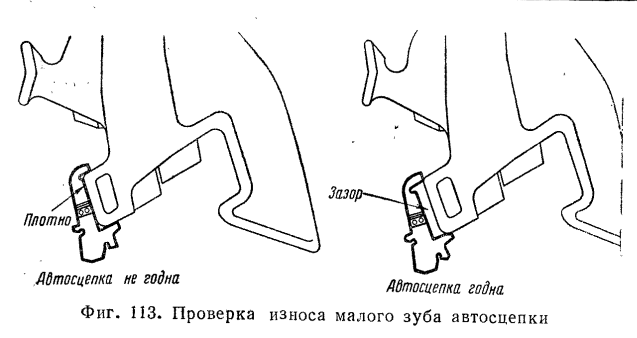
Износ малого зуба проверяется на участке, считая по 80 мм вверх и вниз от продольной оси автосцепки.
Этим же шаблоном производится проверка в поездах расстояния между продольными осями сцепленных автосцепок по вертикали, т. е. разность их высот над головками рельсов, как показано на фиг. 114. Расстояние между опорными гранями выступов 1 и 2 шаблона составляет 100 мм. Для проверки шаблон выступом упирают в низ замка вышестоящей автосцепки. Если при этом между выступом 2 шаблона и низом замка нижестоящей автосцепки будет зазор, то это означает, что разность уровней замков, а следовательно, й автосцепок менее 100 мм (фиг. 114,а). Если же выступ 2 шаблона упирается в низ замка нижестоящей автосцепки, а выступ 1 не доходит до замка вышестоящей, то расстояние между продольными осями автосцепок превышает допускаемые 100 мм (фиг. 114,6). Не допускается определение разности уровней сцепленных автосцепок по верхним кромкам их корпусов, так как в этом случае могут быть допущены ошибки приблизительно на 15 мм из-за разницы в размерах корпусов автосцепок образцов 1935 и 1938 гг.
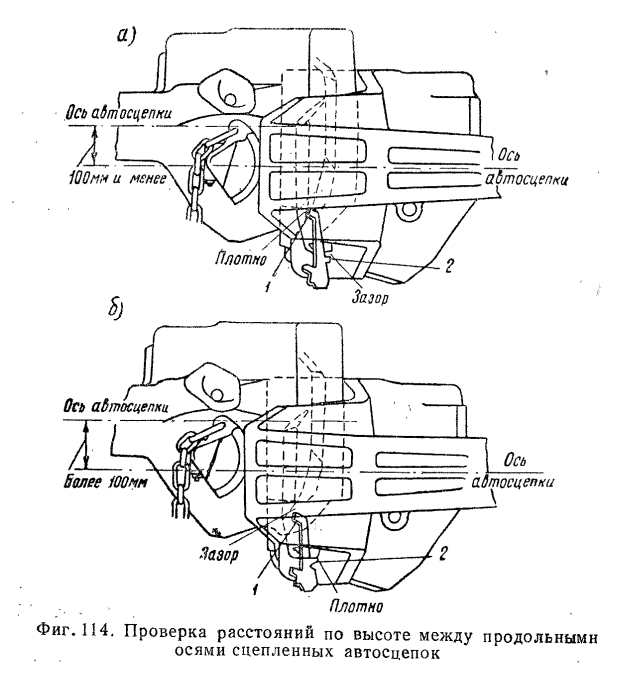
Наряду с этим в эксплуатации может применяться и прежний комбинированный шаблон, показанный на фиг. 115, порядок пользования которым широко известен. У шаблонов Холодова и комбинированного нормы додускаемого технического состояния автосцепки одинаковы.
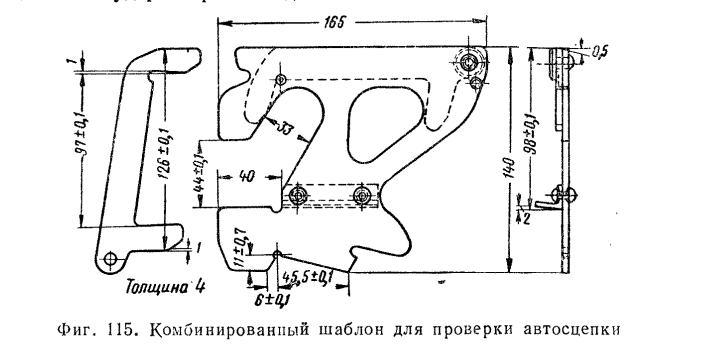
После проверки шаблоном и определения годности автосцепки проверяют правильность установки и крепление валика подъёмника, а также расстояние от упора головы автосцепки до розетки. Валик подъёмника должен быть поставлен так, чтобы балансир был обращён в сторону, противоположную буферному брусу, и закреплён только типовым способом (см. фиг. 20). Расстояние от упора головы автосцепки до наиболее выступающей части ударной розетки должно быть не менее 60 мм и не более 100 мм. Далее осматривается ударная розетка, центрирующий прибор, расцепной привод и упряжное устройство под вагоном.
Особое внимание обращается па состояние клина тягового хомута и его крепление, которое должно быть типовым. Для выявления трещины или излома клина тягового, хомута применяется металлический щуп из проволоки с загнутым концом. При сжатых автосцепках щуп пропускается вдоль клина через зазор между его боковой поверхностью и стенкой отверстия в тяговом хомуте. Если ощущается задевание крючка щупа, то это свидетельствует о наличии трещины или излома клина.
Если клин не зажат между хвостовиком автосцепки и тяговым хомутом, то излом его можно обнаружить ударом ручного молотка снизу, не отрывая последний от клина. При наличии излома будет слышен двойной звук удара.
Косвенным признаком излома клина является изгиб поддерживающего болта, причём клин бывает наклонён чаще в сторону буферного бруса. При тяговом хомуте с ушками под два поддерживающих болта изогнутым обычно бывает болт, расположенный ближе к буферному брусу.
Осмотрщик вагонов станции Кизляр Орджоникидзевской дороги Петрова, а также другие осмотрщики, усвоившие эти признаки, успешно обнаруживают изломанные клинья. Указанные методы обнаружения изломанных клиньев тягового хомута широко применяются осмотрщиками вагонов железных дорог сети.
Сломанный клин опасен тем, что он расклинивает горловину тягового хомута и разрывает боковые вертикальные перемычки его головной части, а также может привести к обрыву тяговой полосы хомута и разрушению буферного бруса.
При осмотре автосцепного устройства одиночных несцепленных вагонов необходимо проверять и при необходимости регулировать длину цепи расцепного привода.
После проверки рукоятку расцепного рычага нужно расположить вертикально, а плоскую часть его опустить в паз кронштейна.
На пунктах технического осмотра осмотр автосцепного устройства в поездах производят осмотрщики вагонов и осмотрщики- пролазчики.
В обязанность осмотрщика-пролазчика входит проверка под вагонами упряжного устройства и между вагонами действия предохранителей от саморасцепа автосцепок.
Порядок осмотра автосцепного устройства вагонов в поездах такой же, как для одиночного несцепленного вагона, за исключением того, что действие предохранительного устройства механизма автосцепки от саморасцепа проверяется специальным металлическим ломиком Коржова, как показано на фиг. 116.
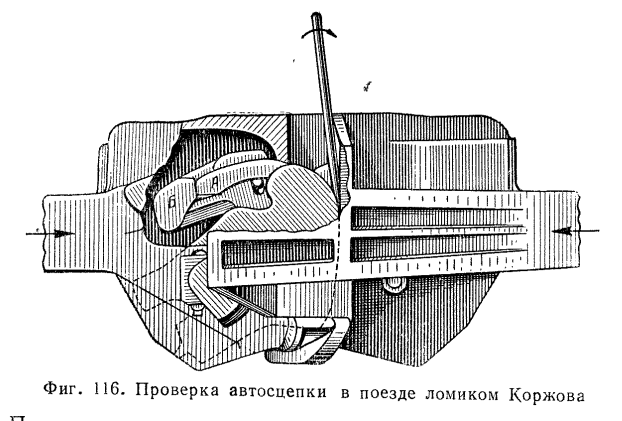
Для проверки ломик заострённым концом заводят сверху в пространство между ударной стенкой зева одной автосцепки и торцовой частью замка смежной автосцепки и нажимают на замок. Если замок не уходит внутрь головы автосцепки и при этом слышен звонкий металлический стук от удара верхнего плеча собачки в противовес замкодержателя, то предохранительное устройство от саморасцепа исправно.
Если же замок от нажатия ломиком свободно уходит внутрь головы автосцепки или же уходит неполностью, но при этом неслышно металлического стука, то предохранитель от саморасцепа неисправен. В этом случае требуется разборка механизма автосцепки для выявления неисправностей и устранения их. Этот способ проверки исправности действия механизма автосцепки легко применим в грузовом поезде. Для проверки автосцепок в пассажирском поезде или у сцепов платформ под общим грузом указанный способ неприменим из-за того, что сверху автосцепки закрыты. В этих случаях применяется способ, предложенный Носковым, заключающийся в том, что ломик заводится снизу кармана головы автосцепки так, чтобы его остриё подошло под замок (фиг. 117).
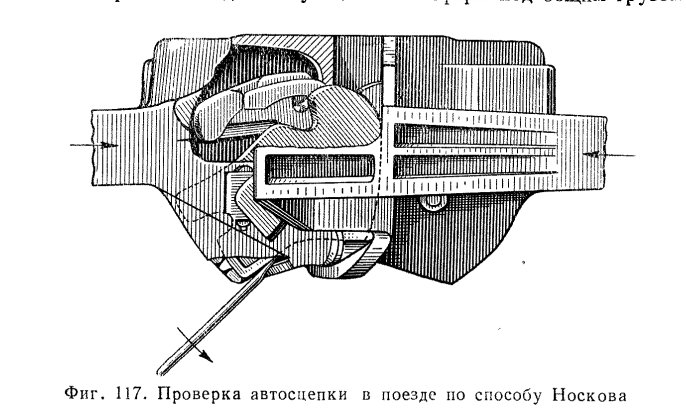
В этом случае, так же как при проверке ломиком Коржова, если замок не уходит в карман головы автосцепки и слышен металлический звук, то предохранитель от саморасцепа автосцепок исправен; если замок уходит в карман автосцепки, то- предохранитель неисправен.
Оба описанных способа проверки исправности действия предохранительного устройства могут быть применимы только в том случае, когда автосцепки не натянуты. При натянутых автосцепках такую проверку произвести нельзя, так как замки зажаты между малыми зубьями и вследствие этого неподвижны. Поэтому на пунктах технического осмотра, где производится осмотр поездов с пролазкой, нужно требовать остановки их в ненатянутом состоянии.
Кроме того, указанные способы проверки действия предохранителя от саморасцепа не дают полных результатов, так как про- 107 изводятся не при наиболее невыгодных условиях его работы. В ненатянутых автосцепках лапа замкодержателя частично или до отказа вжата в полость головы автосцепки. В последнем случае противовес замкодержателя занимает наивысшее возможное положение, т. е. автосцепка наиболее надёжно предохранена от само- расцепа. Однако в поезде при натянутых автосцепках лапа замкодержателя, упирающаяся в малый зуб соседней автосцепки, имеет наибольший выход в зев. При износах тяговых и ударных поверхностей зубьев автосцепки сверх допустимого выход лапы замкодержателя и опускание противовеса его могут быть настолько значительными, что предохранение автосцепок от саморасцепа станет ненадёжным.
Таким образом, оба способа проверки исправности действия предохранительного устройства позволяют обнаружить лишь грубые неисправности автосцепки (излом замкодержателя, излом полочки для верхнего плеча собачки и др.). Такие неисправности в механизме автосцепки, как изгиб полочки, изгиб противовеса замкодержателя в вертикальной и горизонтальной плоскостях, не могут быть обнаружены с помощью ломика. В то же время указанные неисправности могут привести к выключению действия предохранителя от саморасцепа автосцепки вследствие уменьшения площадки перекрытия торца верхнего плеча собачки противовесом замкодержателя.
Поэтому основное внимание должно быть сосредоточено на выявлении и устранении неисправностей автосцепки до включения вагонов в поезда, чтобы исключить необходимость применения дополнительных методов проверки в поездах. На станции Дебальцево Донецкой дороги стали применять предложенный осмотрщиком-пролазчиком В. И. Синеоким новый метод проверки действия механизма автосцепки в поездах. Этот метод заключается в применении остроконечного ломика и специальных крючков, изготовленных из тонкой стальной проволоки. На фиг. 118, а показан ломик для проверки надёжности действия предохранителя от саморасцепа, на фиг. 118, б — фасонный крючок с рисками 1 и 2, которым проверяется возвышение противовеса замкодержателя над полочкой, и на фиг. 118, в— крючок-штан- гомер с риской 3 для измерения расстояния между продольными осями сцепленных автосцепок, определения состояния полочки для верхнего плеча собачки и выявления изогнутого противовеса замкодержателя.
Ломик состоит из стержня 1 (см. фиг. 118,а) с клиновидным концом, головки с металлической щёткой 2 и полого стержня 3, служащего футляром для щётки. На клиновидном конце ломика, там, где Ширина клина равна 20 мм, нанесена риска 4.
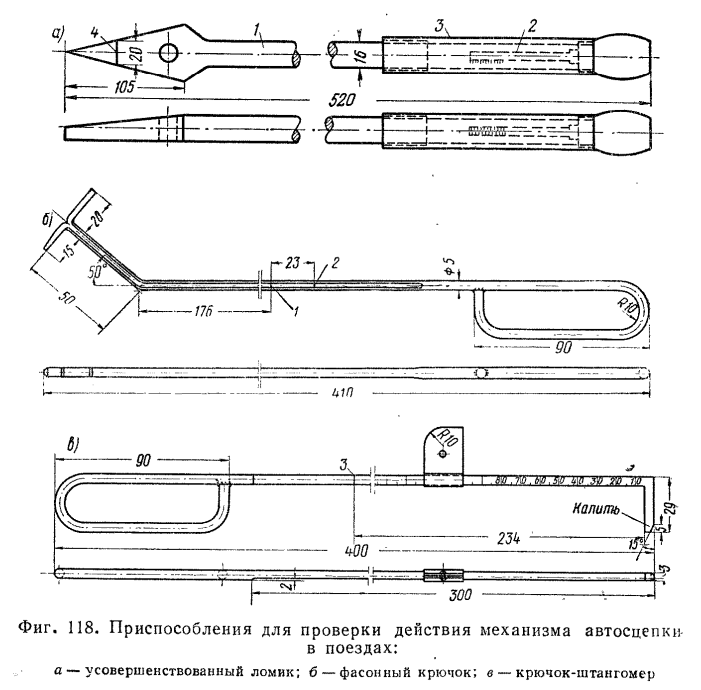
Щётка предназначена для расчистки осматриваемых мест деталей. Для проверки действия предохранителя от саморасцепа ломик вставляют клиновидным концом между ударной стенкой зева одной автосцепки и замком другой. Нажимая ломиком на замок, вталкивают его в корпус и по положению риски определяют, на какое расстояние замок отходит от кромки ударной стенки малого зуба.
Если отход замка от кромки малого зуба превышает 20 мм, то механизм автосцепки подвергается тщательной проверке при помощи крючков.
Для проверки возвышения противовеса замкодержателя над. полочкой фасонный крючок вводится внутрь головы автосцепки через отверстие для сигнального отростка замка и ножкой, имеющей длину 15 мм, зацепляется за полочку, как показано на фиг. 119, а. Если при этом риска / скрылась внутри корпуса, то полочка расположена слишком высоко.
Убедившись в правильном положении полочки, продвигают крючок вверх по стенке корпуса и второй ножкой, имеющей длину 20 мм, зацепляют за противовес замкодержателя (фиг. 119,6). Если при этом риска 2 крючка остаётся снаружи корпуса автосцепки, то величина возвышения противовеса замкодержателя над полочкой недостаточна.
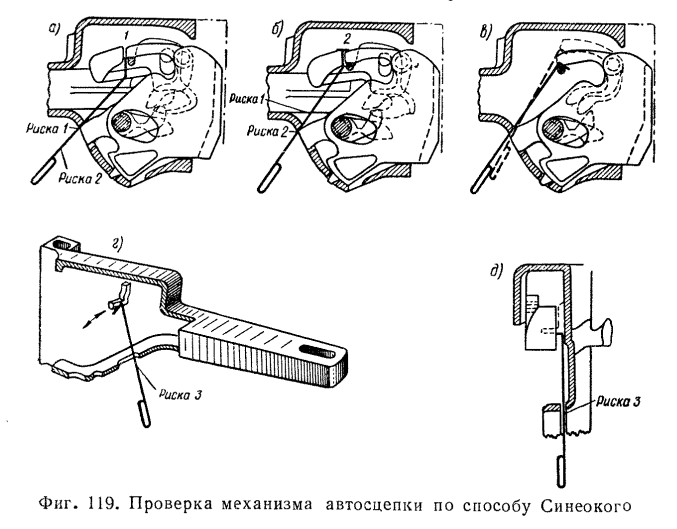
Далее производится дополнительная проверка механизма крючком-штангомером. Для проверки штангомер вводится в полость головы автосцепки через отверстие для сигнального отростка замка, зацепляется ножкой за полочку (фиг. 119, в) и поворачивается вокруг своей оси так, чтобы ножка попала под верхнее плечо собачки. Затем плечо собачки толчком поднимают и сбрасывают с ножки штангомера. Если плечо исправно, то при падении слышен звонкий металлический стук от удара о полочку.
Для проверки изогнутости полочки подводят крючок-штангомер, как показано на фиг. 119, г, и продвигают ножку вдоль полочки. Если полочка изогнута, то ножка штангомера не будет продвигаться от стенки кармана или же стержень штангомера будет выходить из корпуса автосцепки наружу, о чём можно судить по риске 3.
Для проверки изогнутости замкодержателя стержень штангомера прижимают к внутренней стенке кармана головы автосцепки со стороны малого зуба, пропускают вверх до контрольной риски 3 и поворачивают вокруг своей оси на 180°. Если при этом ножка штан- гсмера проходит между стенкой и противовесом замкодержателя, то противовес отогнут в горизонтальной плоскости (фиг. 119,д).
Крючком-штангомером проверяют также разность высот сцепленных автосцепок над головками рельсов. Проверка производится по замкам. Для этого ножку штангомера упирают в нижнюю поверхность замка вышестоящей автосцепки и затем передвигают движок по стержню до упора вниз замка смежной автосцепки. По делениям, нанесённым на стержне, определяют разность высот. Вагоны и локомотивы не допускаются к следованию в поездах, если их автосцепное устройство имеет хотя бы одну из следующих неисправностей:
- высота продольной оси автосцепки над уровнем головок рельсов у грузовых вагонов менее 950 или более 1 080 мм, у пассажирских вагонов менее 980 или более 1 080 мм, у локомотивов менее 980 или более 1 070 мм, у тендеров менее 980 или более 1 090 мм\
- расстояние по высоте между продольными осями сцепленных автосцепок больше 100 мм.;
- расстояние от упора головы автосцепки в свободном состоянии до наиболее выступающей части розетки менее 60 или более 100 мм;
- сцепление двухзвенной цепью двух платформ с общим грузом;
- расстояние между тарелками буферных стержней больше 125 мм при сцеплении вагонов двухзвенной цепью;
- отсутствие скобы под крюком типа, применяемого на тендерах паровоза серии ФД;
- трещина в корпусе автосцепки, излом деталей механизма;
- недействующий предохранитель от саморасцепа автосцепок;
- износы рабочих поверхностей контура зацепления и уширение зева сверх допускаемых размеров при измерении комбинированным шаблоном Холодова;
- отсутствие валика подъёмника автосцепки или валик, не закреплённый от выпадения, закреплённый нетиповым способом или неправильно поставленный;
- трещина или излом в любой части тягового хомута или его клина;
- неисправное или нетиповое крепление клина тягового хомута;
- неисправности поглощающего аппарата, угрожающие падению его частей или вызывающие полную потерю упругих свойств;
- излом или трещина балочки или маятниковой подвески центрирующего прибора, неправильно поставленные маятниковые подвески (широкими головками вниз);
- трещина или излом поддерживающей планки, кронштейна или державки расцепного привода, ударной розетки, упорных угольников, паровозной розетки;
- короткая цепь расцепного привода, не прикрученные проволокой к кронштейнам рукоятки расцепных приводов при перевозке общего груза на двух платформах.