Назначение рельсов — создать поверхности с наименьшими сопротивлениями для качения колес подвижного состава, непосредственно воспринимать и упруго передавать воздействия колес на опоры (шпалы, брусья и т.п.) и направлять колеса подвижного состава. На участках с автоблокировкой рельсовые нити служат также проводниками сигнального тока, а на участках с электрической тягой — обратного тягового тока.
Рельсы должны быть достаточно прочными, долговечными, надежными в эксплуатации, твердыми и одновременно вязкими (нехрупкими), так как они воспринимают ударно-динамические нагрузки.
Масса рельсов, поперечные профили, химический состав рельсовой стали и технология изготовления взаимосвязаны и в совокупности определяют эксплуатационные качества рельса как элемента верхнего строения пути.
С 1 июля 2001 г. введен в действие Государственный стандарт Российской Федерации ГОСТ Р 51685-2000 «Рельсы железнодорожные.
Общие технические условия». Объектом стандартизации являются рельсы типов Р50, Р65, Р65К и Р75, термически обработанные по всей длине и нетермоупрочненные, предназначенные для укладки в бесстыковом и звеньевом пути железных дорог широкой колеи, а также для производства элементов стрелочных переводов. ГОСТ Р 51685-2000 предусматривает четыре категории качества рельсов: термообработанные — категории В, Т1 и Т2; нетермообработанные — категории Н.
В Государственном стандарте нормируют:
- размеры поперечного сечения и допуски на основные размеры рельса;
- расположение, число и диаметр болтовых отверстий;
- длину рельса и допуски по длине;
- качество отделки болтовых отверстий и торцов рельсов;
- кривизну рельсов;
- химический и газовый состав рельсовых сталей;
- макроструктуру, наличие флокенов и неметаллических включений в рельсовой стали;
- виды и размеры поверхностных дефектов рельсов;
- показатели механических свойств;
- твердость по поверхности и сечению термически упрочненных рельсов, изменчивость твердости по длине рельса; стойкость при копровых испытаниях; величины остаточных напряжений; микроструктуру.
Основные признаки, характеризующие рельсы:
тип рельса — Р50, Р65, Р65К (для наружных нитей кривых), Р75;
категория качества — В — (рельсы термоупрочненные высшего качества), Т — (рельсы термоупрочненные), Н — (рельсы нетермоупроч- ненн ые);
наличие болтовых отверстий (с отверстиями на обоих концах рельсов, без отверстий);
способ выплавки стали — М (из мартеновской стали), К (из конвертерной стали), Э (из электростали);
вид исходных заготовок (из слитков, из непрерывно-литых заготовок);
способпротивофлокенной обработки (из вакуумированной стали, прошедшие контролируемое охлаждение или прошедшие изотермическую выдержку);
длина — рельсы обычной длины, длинные рельсы и рельсовые плети бесстыкового пути.
Типы, профили и длина рельсов
Форма и основные размеры поперечного сечения рельсов приведены на рис. 2.2 и в табл. 2.4.
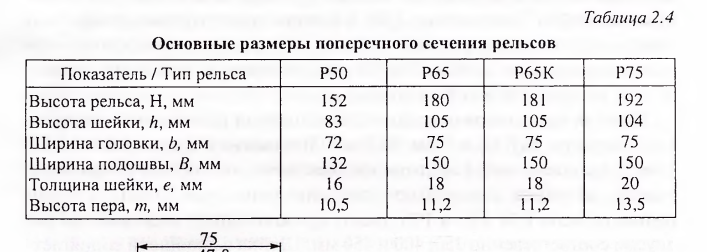

Поперечный профиль рельса должен обеспечивать наибольшую выносливость в процессе эксплуатации, быть удобным для проката на рельсопрокатных заводах и размещения конструкции стыковых скреплений. Рельс имеет профиль двутавровой балки, верхней полке которой придана форма головки. Поверхность катания имеет выпуклое криволинейное очертание. Среднюю часть головки прокатывают по радиусу 500 мм, переходящему в радиус 80 мм и затем в радиус 15 мм. Боковые грани головки делают наклонными 1:20, а нижние грани головки и верхнюю поверхность подошвы рельса — 1:4, как и опорные поверхности стыковых накладок. При затяжке болтов накладки входят как клин в пазуху рельса, распирая головку и подошву.
Нижняя часть головки сопрягается с шейкой рельса двумя радиусами — верхним 5 (Р50) и 7 мм (Р65 и Р75) и нижним соответственно 12; 15 и 17 мм с тем, чтобы местные напряжения при переходе от широкой головки к тонкой шейке были возможно меньшими. Боковые грани шейки рельсов Р50, Р65 и Р75 имеют криволинейное очертание по радиусам соответственно 350, 400 и 450 мм. Шейка с подошвой сопрягается по радиусу большему, чем с головкой: 20 мм (Р50) и 25 (Р75 и Р65).
Современные рельсы имеют круглые отверстия диаметрами 36± 1 мм для болтов (рис. 2.3). Болтовые отверстия по концам рельсов просверливают перпендикулярно к их вертикальной продольной плоскости; заусенцы и наплывы металла у болтовых отверстий и на торцах рельсов удаляют зачисткой.
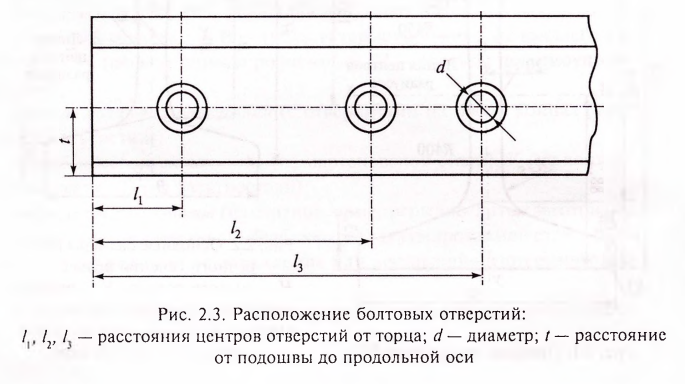
Концы рельсов фрезеруют перпендикулярно продольной оси рельса; перекос в торце не должен быть более 1,0 мм при измерении в любом направлении. На кромках в торце рельсов допускается снимать фаски шириной: до 3 мм — по контуру головки и шейки; до 5 мм — по контуру подошвы. На термоупрочненных рельсах с болтовыми отверстиями обязательно снимают фаски на торцах рельсов по верхней и нижней кромкам головки.
Расстояние от торца рельса до первого отверстия у рельсов Р75 и Р65 равно 96 мм, между осями первого и второго отверстия — 220 мм и от оси второго до оси третьего отверстия — 130 мм; у рельсов Р50 эти расстояния составляют соответственно 66, 150 и 140 мм. Все расстояния имеют допуски ± 1 мм (для рельсов категории В — ± 0,8 мм).
Длина стандартного рельса равна 25 м. Рельсы длиной 12,5м используют в качестве уравнительных на бесстыковом пути, при укладке стрелочных переводов и как инвентарные при сборке путевой решетки с железобетонными шпалами с последующей заменой их бесстыковыми рельсовыми плетями.
Для укладки на внутренних нитях кривых изготовляют укороченные рельсы длиной 24,84 и 24,92 м при 25-метровых рельсах и 12,42 и 12,46 м при 12,5-метровых, а для бесстыкового пути — 12,38 м.
Следующие требования предъявляют к прямолинейности рельсов: стрела прогиба рельсов в горизонтальной и вертикальной плоскостях при равномерной кривизне по всей длине не должна превышать 1/2500 длины рельса категории В; 1/2200 длины рельса категории Т1, Т2 и Н. Отклонения рельсов от прямолинейности по поверхности катания головки в вертикальной плоскости и по боковой грани головки в горизонтальной плоскости на базовой длине 1,5 м при измерении по хорде не должны соответственно превышать 0,3 и 0,5 мм для рельсов категории В; 0,6 и 0,8 — для категорий Т1,Т2 и Н. Скручивание рельсов не должно превышать 1/25 000 длины рельсов категории В; 1/10 000 длины рельса — для категорий Т1,Т2 и Н.
Технология изготовления и химический состав рельсовой стали
До начала 1980 гг. рельсы получали прокаткой из стальных слитков. Для их изготовления применяли сталь двух видов: мартеновскую и бессемеровскую (конверторную). Исходным материалом для выплавки стали являлись чугун и стальной лом при мартеновском процессе и чугун при бессемеровском.
С 1983 г. производство рельсов по бессемеровскому способу прекращено.
Согласно ГОСТ Р 51685-2000 рельсы изготовляют из спокойной стали мартеновского, конверторного или электропечного производства. Содержание углерода в рельсовой стали находится в пределах 0,71 — 0,82 %; в чугуне — до 4 %. Чугун содержит также 1,5—3,5 % марганца; 1,5—2 % кремния, а также фосфор, серу и другие примеси, содержание которых в стали должно быть существенно уменьшено. Основная задача при переплавке чугуна в сталь заключалась в удалении значительной части углерода, марганца, кремния, серы и фосфора.
Химический состав рельсовой стали должен соответствовать установленным ГОСТом параметрам.
Современные рельсы из сталей разных марок содержат: углерод (0,71—0,82 %), марганец (0,75—1,05 %), кремний (0,25—0,80 %), ванадий (0,03-0,15 %), титан (0,007-0,025 %), хром (0,40-0,60 %). Фосфора должно содержаться не более 0,025—0,035 %, серы — не более 0,025— 0,040 %, алюминия — не более 0,05—0,025 %.
Содержание углерода влияет на твердость и износостойкость рельсовой стали. Верхние пределы содержания углерода позволяют избежать увеличения хрупкости стали и возникновения поверхностных дефектов, раковин, плен и т.п. Рельсы с содержанием углерода выше среднего относят к твердым; рельсы из стали, содержание углерода в которых равно или ниже среднего значения, — к нормальным.
Марганец также повышает твердость и износостойкость стали, увеличивая одновременно и ее вязкость. Кремний в указанных ограниченных количествах увеличивает твердость металла. Небольшая примесь меди несколько повышает коррозионную стойкость стали.
Фосфор и сера — примеси вредные. При большом содержании фосфора рельсы становятся хрупкими, а при большом содержании серы могут появиться трещины при прокате (т.н. красноломкость).
Готовую сталь разливают в формы (изложницы), в которых она застывает в виде слитков. Слитки перед прокатом помещают в специальные нагревательные колодцы для подогрева. Разогретый слиток стали обрабатывают вначале на блюминге, придавая слитку форму прямоугольной болванки (т.н. блюмс).
Блюмс передают далее в прокатный стан, где он проходит через валки из ручья в ручей. При этом блюмс вытягивается в длину и постепенно меняет форму, принимая по выходе из последнего ручья профиль за- 130 данных размеров. Полученную полосу разрезают на куски нормальной длины, производят выправку отдельных искривлений, высверливают отверстия для болтов.
В стандарте ГОСТ Р 51685-2000 введено понятие «рельсы высшей категории» В, которые изготавливают из хромистой стали и обязательно подвергают термическому упрочнению. Специальный профиль предусмотрен для рельсов, эксплуатируемых в наружных нитях кривых участков пути.
Расширены возможности производства рельсовой стали с использованием прогрессивных способов ее выплавки, разливки и рафинирования.
Наряду с единственным применявшимся ранее способом выплавки стали в мартеновских печах включена выплавка в кислородных конверторах и электропечах; кроме разливки в слитки применяют непрерывную разливку стали, вакуумирование.
Новым стандартом введены единые для всех типов рельсов нормы по содержанию углерода и кремния; уточнены нормы содержания ванадия и титана; ужесточены нормы остаточного содержания хрома, никеля и меди; введена норма на содержание алюминия и т.п. Впервые введена дифференцированная по категориям качества норма по газовому составу рельсовых сталей (содержанию кислорода и водорода).
Поверхность современного рельса должна быть без раскатанных загрязнений, трещин, рванин, плен, закатов, раковин от окалины, вмятин, поперечных рисок и царапин.
Маркировка новых рельсов
Все новые рельсы маркируют на заводах-изготовителях, что обеспечивает контроль качества рельсов при их изготовлении и эксплуатации. Заводская маркировка рельсов выполняется постоянной — клеймение и временной — красками. На шейке каждого рельса в горячем состоянии выкатывают с одной стороны выпуклую маркировку, содержащую: обозначение предприятия-изготовителя (например, К — Кузнецкий металлургический комбинат, Т — Нижнетагильский металлургическийкомбинат); месяц (римскими цифрами) и год изготовления (арабскими цифрами); тип рельса; обозначение направления прокатки стрелкой (острие стрелки указывает на передний конец рельса по ходу прокатки).
Маркировочные знаки высотой от 30 до 40 мм выступают на 1—3 мм с плавным переходом к поверхности шейки. Маркировку наносят не менее чем в четырех местах (на рельсах длиной 12,5 м — не менее чем в двух местах) по длине рельса.
На шейке каждого рельса на той же стороне, на которой выкатаны выпуклые маркировочные знаки, в горячем состоянии клеймением наносят: шифр плавки, условное обозначение контрольных рельсов; условное обозначение термоупрочненных рельсов. Маркировочные знаки высотой около 12 мм и глубиной 0,8—1,5 мм располагают на расстоянии 20—40 мм друг от друга. Шифр плавки включает обозначение способа выплавки для конвертерного (К) и электропечного (Э) производства стали; условное обозначение стали (X — низколегированная, V — мик- ролегированная ванадием, Т — микролегированная титаном); обозначение сталеплавильного агрегата и порядковый номер плавки.
На один из торцов рельса в холодном состоянии клеймением наносят: шифр плавки — на подошве; условное обозначение контрольного рельса — на верхней четверти шейки; знаки закалки концов рельсов (букву К) — на нижней четверти шейки рельса.
На торец головки каждого принятого рельса наносят приемочные клейма: ОТК завода-изготовителя; инспекции по путевому хозяйству ОАО «РЖД» или другого потребителя по его требованию.
Маркировку наносят несмываемой краской: голубого цвета — на рельсах категории В; фисташкового (светло-зеленого) цвета — на рельсах категории Т1; желтого цвета — на рельсах категории Т2; белого цвета — на рельсах категории Н.
Маркировку наносят на торце рельса — обведением контура головки с приемочными клеймами; на поверхности головки и шейки рельса — поперечной полосой шириной 15—30 мм на расстоянии 0,5—1,0 м от торца с приемочными клеймами.
Пример маркировки новых рельсов приведен на рис. 2.4.
На рельсосварочных предприятиях рельсы длиной 25 м сваривают в плети длиной до 800 м. Сварные стыки отмечают на шейке рельса внутри колеи двумя вертикальными полосами симметрично относительно оси стыков на расстоянии 10 см от них. В середине плети на шейке рельса наносят вертикальную полосу.
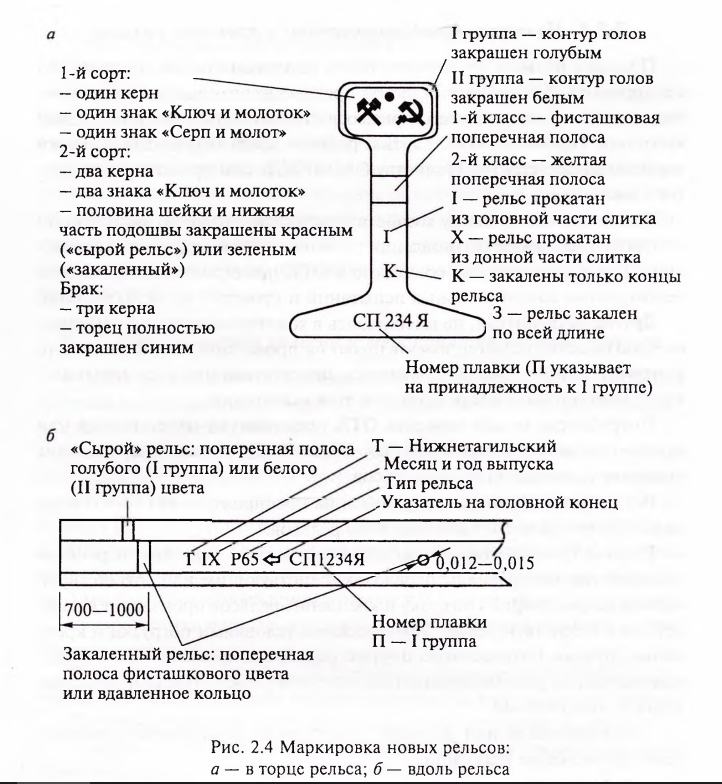
В начале и конце каждой плети белой масляной краской на внутренней стороне шейки рельса (со стороны оси пути) указывают номер рельсосварочного предприятия, номер плети по сварочной ведомости, длину плети в метрах с точностью до второго знака после запятой. Длину плети L указывают при температуре рельсов + 20 °С.
Приемка, транспортировка и хранение рельсов
Приемку рельсов производит отдел технического контроля (ОТК) предприятия-изготовителя. Приемку производят по результатам приемочного контроля, включающего приемосдаточные испытания и сплошной контроль. Принятую ОТК партию рельсов предъявляют для приемки инспекции по путевому хозяйству ОАО «РЖД» или представителю другого заказчика.
Инспекции по путевому хозяйству предоставлено право выборочного контроля технологии изготовления рельсов, отбора проб от рельсов любой плавки и проведения совместно с ОТК предприятия-изготовителя необходимых дополнительных испытаний и проверки качества рельсов.
Другие потребители, не вмешиваясь в ход технологического процесса производства рельсов, имеют право на проведение инспекционного контроля технологического процесса, присутствие при всех испытаниях рельсов и получение результатов этих испытаний.
Потребитель может передать ОТК предприятия-изготовителя или инспекции по путевому хозяйству ОАО «РЖД» право на проведение контроля и приемки партии рельсов.
Все результаты контроля хранятся на предприятии-изготовителе не менее 20 лет с момента изготовления рельсов.
Рельсы транспортируют железнодорожным, морским и речным транспортом по правилам перевозок, действующим на соответствующем виде транспорта. Погрузку и крепление рельсов производят в соответствии с действующими «Техническими условиями погрузки и крепления грузов». Отгружаемую партию рельсов сопровождают документом о качестве, удостоверяющем соответствие рельсов требованиям стандарта и содержащим:
- наименование или условное обозначение предприятия-изготовителя; обозначение стандарта;
- тип рельсов;
- категорию рельсов; марку стали;
- отпечатки или описание приемочных клейм инспекции ОАО «РЖД» (или другого потребителя) и описание маркировки рельсов красками;
- число рельсов с указанием их длины и массы;
- дату оформления документа о качестве рельсов;
- номер вагона или другого транспортного средства;
- наименование и адрес покупателя;
- номер заказа (договора).
Документ о качестве рельсов должен быть подписан ОТК предприятия-изготовителя, а рельсов, отгружаемых для ОАО «РЖД», и инспекцией по путевому хозяйству ОАО «РЖД».
При погрузке и транспортировании рельсов не допускается повреждение рельсов. Не допускается падение рельсов с высоты более 1 м. Рельсы, упавшие с высоты более 1 м, считают несоответствующими требованиям стандарта. В период хранения рельсы должны быть уложены таким образом, чтобы не возникали деформации и ухудшение прямолинейности рельсов.
Сроки службы рельсов и мероприятия по их продлению
Рельсы в процессе эксплуатации по мере роста пропущенного по пути тоннажа повреждаются и стареют. В рельсах образуются дефекты, вызывающие отказы их работы.
Рельсы изымаются по двум основным причинам: износ головки рельса до предельно допускаемой величины (около 3 % изымаемых рельсов); одиночный выход рельсов по дефектам, измеряемый в штуках на км. Головка рельса может иметь и боковой износ (по ширине головки), который измеряется на уровне 13 мм ниже поверхности катания. Боковой износ приравнивают к вертикальному износу в половинном размере, т.е. 1 мм бокового износа приравнивают к 0,5 мм вертикального износа.
Сумму вертикального и половины бокового износа называют приведенным износом.
Износ рельсов — результат истирания головок рельсов в процессе их взаимодействия с колесами подвижного состава и окружающей средой.
Интенсивность износа рельсов зависит от следующих факторов:
- окружных усилий, передаваемых колесами, и проскальзывания колес по рельсам;
- давления колес на рельсы и пропущенного по ним тоннажа;
- масс и скоростей движения поездов;
- плана и профиля пути;
- конструкции пути и подвижного состава;
- профилей контактирующих поверхностей колес и рельсов;
- от качества металла колес и рельсов и др.

Вертикальный износ определяют как разность между высотой рельса по ГОСТу и высотой рельса, измеренной штангенциркулем по оси рельса.
Боковой износ определяют как разность между шириной головки по ГОСТу на уровне 13—15 мм ниже поверхности катания и фактической шириной головки, измеренной на том же уровне.
На отечественных железных дорогах установлены предельно допустимые величины износа рельсов, дифференцированные в зависимости от типа рельсов, категории пути, условий эксплуатации участка (табл. 2.5).
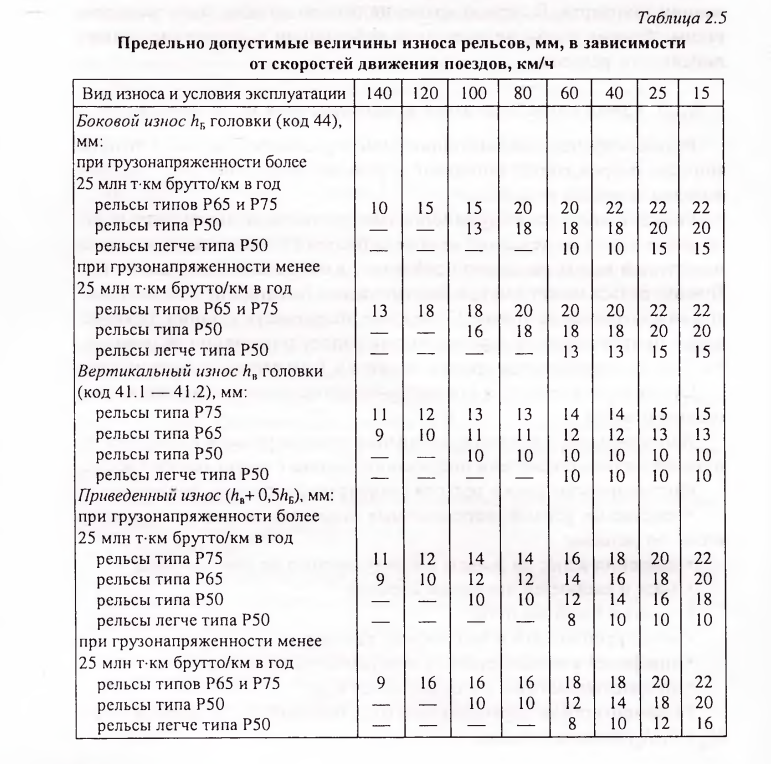
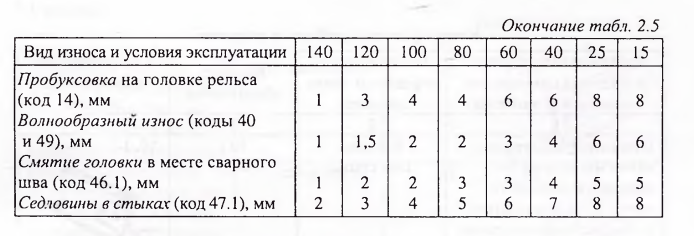
При превышении допустимого износа рельсы считаются дефектными.
Дефекты рельсов характеризуются изменениями геометрических форм или качественных свойств рельсов, соблюдение которых обеспечивает их работоспособное состояние.
К дефектам рельсов относят: трещины, отслоения и выкрошивания рельсового металла, все виды износа, величины которых превышают нормированные значения, пластические деформации в виде смятия, сплывов металла головки рельса, коррозии, механических повреждений.
Классификация дефектов рельсов изложена в трех документах. Первый документ «Классификация дефектов рельсов» (НТД/ЦП-1-93) объясняет структуру кодового обозначения дефектов рельсов; второй — «Каталог дефектов рельсов» (НТД/ЦП-2-93) дает описание каждого дефекта с его изображением, способы выявления и указания по эксплуатации дефектных рельсов; третий — определяет «Признаки дефектных и остродефектных рельсов» (НТД/ЦП-3-93).
Опытную проверку на железных дорогах проходит «Нормативно-техническая документация НТД/ЦП 2002», в которой содержатся виды дефектов рельсов, причины их возникновения, способы выявления и указания по техническому обслуживанию дефектных рельсов. В последующем изложении использованы основные положения НТД/ЦП 2002.
Описание (классификация) дефектов рельсов с кодовым обозначением и схематическим изображением приведено в табл. 2.6. В классификации каждый дефект кодируется трехзначным числом (кодовое обозначение).
Первая цифра кода определяет вид дефекта рельсов и место его расположения по сечению рельса (головка, шейка, подошва).
Вторая цифра кода определяет разновидность дефекта с учетом основной причины его зарождения и развития. Первые две цифры кода дефектов рельсов отделяются от третьей цифры точкой.

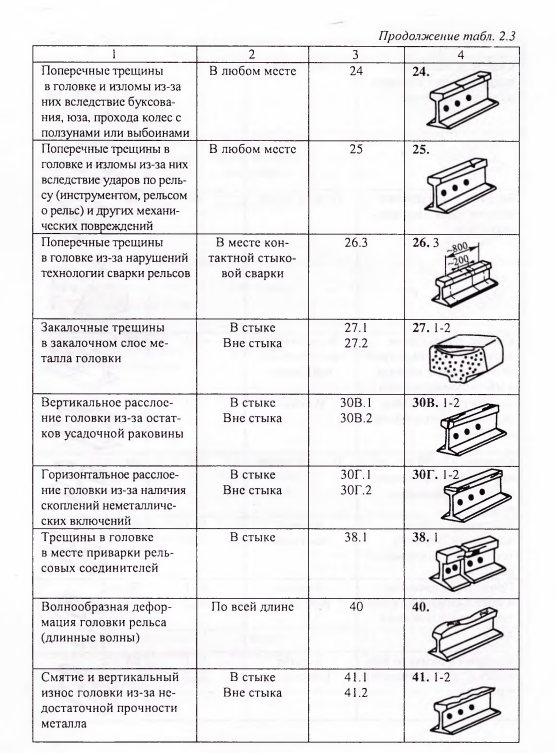
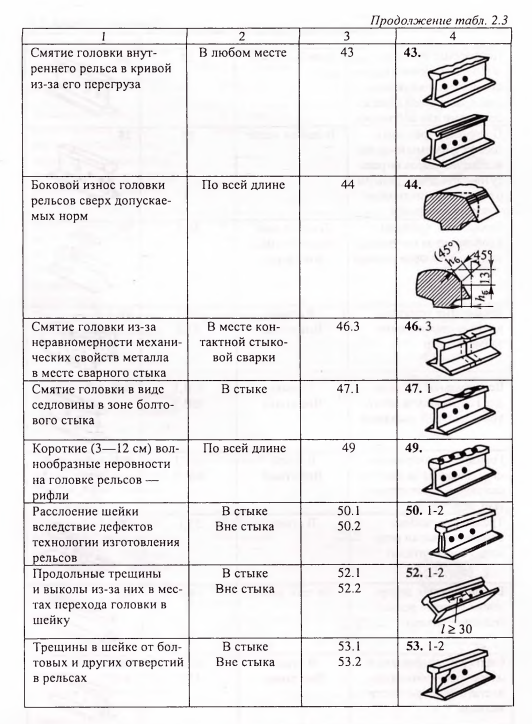
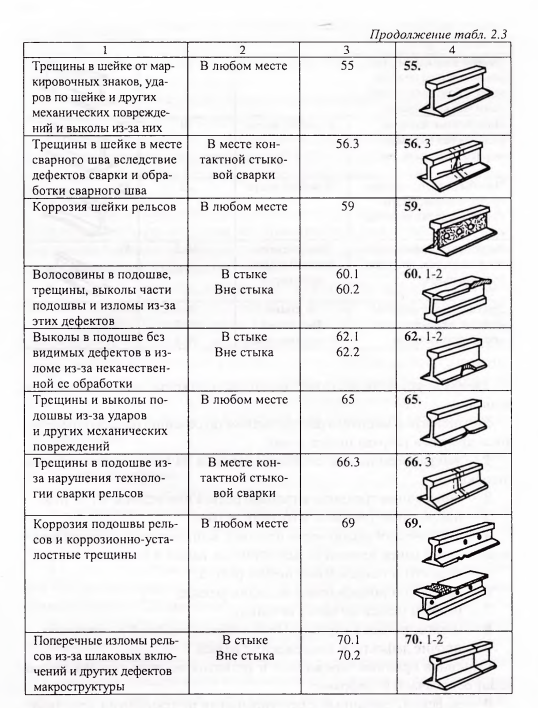
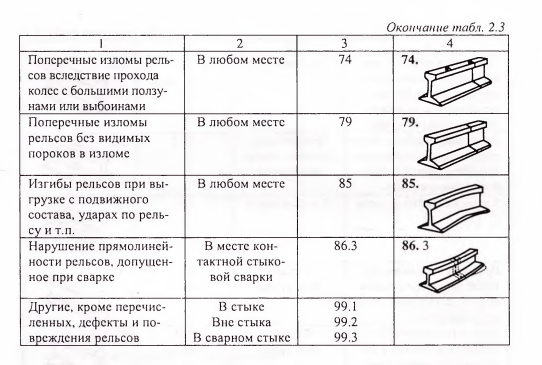
Третья цифра кода указывает место расположения дефекта по длине рельса.
Вид дефекта и место его расположения по сечению рельса определяются цифрами (первая цифра кода):
- — выкрашивание или отслоение металла на поверхности катания головки;
- — поперечные трещины в головке рельса или изломы из-за них;
- — продольные трещины в головке рельса;
- — пластические деформации (смятие), вертикальный, боковой и неравномерный износ головки рельса (длинные волны и короткие рифли);
- — дефекты и повреждения шейки рельса;
- — дефекты и повреждения подошвы рельса;
- — изломы рельса по всему сечению;
- — изгибы рельса в вертикальной и горизонтальной плоскостях;
- — прочие дефекты и повреждения рельса.
Основная причина зарождения и развития дефекта (вторая цифра кода) обозначается цифрами:
О — дефекты, связанные с отступлениями от технологии производства рельсов;
- — дефекты, зависящие от металлургического качества рельсовой стали (местных неметаллических включений в виде дорожек- строчек) и от недостаточной контактно-усталостной прочности рельсового металла;
- — дефекты, связанные с некачественной обработкой торцов и недостатками исполнения профиля рельса;
- — дефекты, связанные с нарушениями требований Инструкции по текущему содержанию железнодорожного пути, а также с нарушениями технологии обработки болтовых отверстий рельсов на металлургических комбинатах;
- — дефекты, связанные со специфическим воздействием подвижного состава на путь (ползуны, юз, буксование и др.), в том числе из-за нарушения режимов вождения поездов или недостатков в содержании экипажной части подвижного состава;
- — дефекты рельсов, полученные в результате механических воздействий на рельсы (удар инструментом, рельсом о рельс и т.п.);
- — дефекты в зоне сварных стыков, связанные с недостатками и нарушениями технологии сварки рельсов;
- — дефекты, связанные с особенностями работы рельсов в стыках;
- — дефекты, связанные с недостатками и нарушениями технологии наплавки рельсов или приварки рельсовых соединителей;
- — дефекты, вызванные коррозией или другими не перечисленными причинами.
Место расположения дефекта по длине рельса (третья цифра кода) обозначается цифрами:
- — по всей длине рельса;
- — дефект располагается в стыке: в болтовом — на расстоянии 750 мм от торца рельса; в сварном стыке — на расстоянии 200 мм симметрично по 100 мм в обе стороны от оси сварного шва;
- — дефект расположен вне стыка: в болтовом — на расстоянии более 750 мм от торца рельса; в сварном стыке — на расстоянии 440 мм симметрично по 220 мм по обе стороны от оси сварного шва.
Рельсы в зависимости от вида повреждения и дефекта подразделяют на дефектные (Д) и остродефектные (ОД).
Остродефектный рельс (ОД) представляет прямую угрозу безопасности движения поездов из-за возможного разрушения непосредственно под колесами или схода колес с рельса из-за повреждения и подлежит немедленному изъятию (замене) после обнаружения.
Основными признаками остродефектных рельсов в главных и приемоотправочных путях считают:
- поперечные, продольные или наклонные (видимые или внутренние) трещины в головке рельсов, независимо от их размера, в основном, дефекты второй и третьей групп (коды 20; 21; 24; 25; 26.1; 30; с продольной горизонтальной трещиной на глубине более 8 мм; 31; 38), а также поперечные трещины (коды 10;11; 14; 16.1; 18; 19);
- продольные трещины и выколы из-за них в местах перехода головки в шейку, начинающиеся с торца с одной или двух сторон шейки, независимо от их размера (см. табл. 2.6, код 52.1), а также рельсы с трещинами длиной более 30 мм, расположенными вне концов рельсов (код 52.2);
- трещины от болтовых отверстий (код 53) и трещины в шейке рельса независимо от их размеров (коды 50, 55 и 56.1 и 59);
- местный износ или коррозия кромки подошвы рельсов (код 69), в том числе трещины коррозионно-усталостного происхождения, выколы части подошвы рельса (дефекты 60, 64, 65, 66); поперечный излом рельса (коды 70, 71, 73, 74, 75, 76, 79).
По остродефектным рельсам с трещинами без полного излома возможен пропуск отдельных поездов со скоростью не более 15 км/ч, в необходимых случаях — с проводником. По рельсам Р65 и Р75 с внутренними трещинами, не выходящими на поверхность, разрешается пропуск поездов со скоростью до 25 км/ч. По рельсам с поперечным изломом или выколом части головки без принятия специальных мер пропуск поездов не допускается.
Дефектный рельс (Д) характеризуется постепенным снижением служебных свойств, что в отдельных случаях может приводить к необходимости снижения скоростей движения поездов.
Основными признаками дефектных рельсов в главных и приемо-отправочных путях считают:
- превышение нормативного приведенного (код 41-44), бокового (код 44) или вертикального износа головки рельса;
- выкрошивание металла глубиной более 3 мм и длиной более 25 мм;
- пробуксовки от колес локомотивов, волнообразный износ, седловины в стыках.
Дефектные рельсы по НТД/ЦП 2002 подразделяют на четыре типоразмера в зависимости от степени развития дефекта: ДП (наиболее опасный), Д1, Д2, ДЗ. Для каждого типоразмера устанавливается предельная скорость движения: не более 40, 70, 100 км/ч для типоразмеров ДП, Д1, Д2 соответственно и без ограничений — для ДЗ. Дефектные рельсы заменяют в плановом порядке.
Маркировку дефектов рельсов при осмотрах и проверках остродефектных и дефектных рельсов производят следующим образом (рис. 2.5).
На шейке рельса с внутренней стороны колеи на расстоянии около 1 м от левого стыка светлой масляной краской наносят косые кресты: один — на дефектном рельсе; два — на остродефектном. После косого креста на остродефектном рельсе наносят знаки П, 1,2, 3; на дефектном рельсе — соответственно ДП, Д1, Д2 или ДЗ.
На шейке рядом с дефектом стой стороны, с которой он виден (или всегда с внутренней стороны колеи, если дефект обнаружен дефектоскопными средствами), повторяют два косых креста для остродефектных рельсов и один косой крест для дефектных рельсов с указанием через наклонную черту кода дефекта.
При распространении дефекта по всей длине рельса в середине рельса указывается его код с черточками с обеих сторон от него (например, -41.2-); при дефекте на левом конце рельса в пределах 75 см от стыка (рис. 2.6), код дефекта ставят рядом с первой маркировкой; вторую маркировку не делают. При расположении дефекта на правом конце рельса в пределах 75 см от стыка на нем дополнительно к маркировке на левом конце рельса наносится маркировка с указанием кода дефекта.
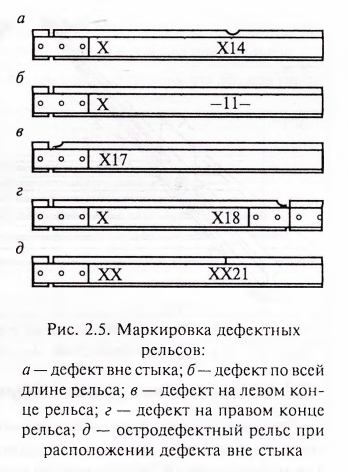
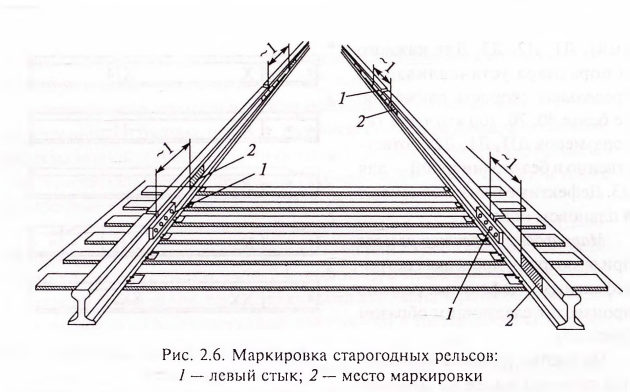
Старогодные рельсы. Маркировка старогодных рельсов
Группы годности старогодных рельсов позволяют определить возможность и сферы повторного использования в пути старогодных рельсов и рельсовых плетей, изымаемых из пути при всех видах ремонта, сплошной или одиночной замене и при текущем содержании.
Повторная укладка старогодных рельсов в путь возможна без ремонта и с ремонтом, в том числе с профильной обработкой головки в рельсосварочных предприятиях (РСП) или в пути рельсошлифовальными поездами (РШП).
Группа годности рельсов устанавливается на месте их изъятия из пути, а отремонтированных в РСП или в пути РШП — после завершения ремонта.
Основным критерием отнесения термоупрочненных рельсов типов Р65 и Р75 к определенной группе годности независимо от конструкции, класса, группы и категории пути, с которого рельсы сняты, является нормативная наработка тоннажа Т . Нормативная наработка составляет для рельсов первой укладки типа Р65 — 600 млн т брутто (звеньевой путь) и 700 млн т брутто (бесстыковой путь); для рельсов Р75 соответственно 700 и 800 млн т брутто (табл. 2.7). Для нетермоупрочненных рельсов Р65 и Р75 нормативная наработка тоннажа уменьшается в 1,5 раза. Для рельсов Р50 и легче нормативная наработка тоннажа составляет 400 млн т брутто.
К IV группе годности относят рельсы, не вошедшие в I, II, Ш группы годности, которые невозможно или экономически нецелесообразно привести в состояние, позволяющее укладывать их в путь.
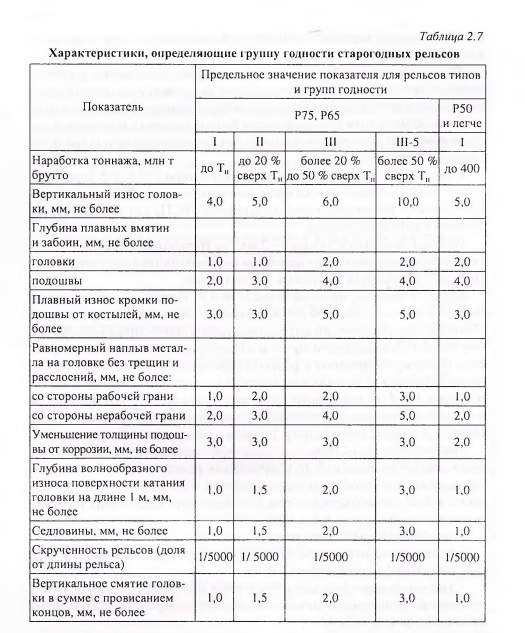
К таким рельсам относят: рельсы Р43 и легче; рельсы, длина годного куска которых менее 6 м; рельсы, переложенные с переменой рабочего канта и имеющие предельные величины бокового и вертикального из- 147 носов. Рельсы IV группы используют для изготовления противоугонов, кузнечных изделий и т.п.
Технические требования к старогодным рельсам установлены в зависимости от группы годности, объема и места проведения мероприятий по восстановлению их служебных свойств перед повторной укладкой в путь.
Снимаемые с пути рельсы должны быть осмотрены, обмерены и замаркированы с разделением каждого типа рельсов на группы годности с учетом термоупрочнения.
Старогодные термоупрочненные рельсы типов Р65 и Р75 всех групп годности без бокового износа или с боковым износом 3 мм и менее направляются в рельсосварочное предприятие (РСП) для ремонта с профильной обработкой головки.
Рельсы с боковым износом 1—3 мм, не требующие вырезки дефектных мест, укладываются без перемены рабочего канта в наружные нити кривых участков пути радиусами 650 м и менее.
Рельсы с боковым износом более 3 мм в РСП не направляют, а укладывают в путь с переменой рабочего канта с соблюдением требований «Технических указаний по перекладке термоупрочненных рельсов типов Р65 и Р75 в звеньевом пути» и «Технических указаний по устройству, укладке, содержанию и ремонту бесстыкового пути». Если требования Технических указаний не выполняются, рельсы с боковым износом более 3 до 8 мм укладывают в наружные нити кривых радиусами 650 м и менее без перемены рабочего канта; с боковым износом более 8 мм до 18 мм — в прямые участки пути 5 класса с переменой рабочего канта.
Требования к старогодным рельсам, перекладываемым на другие участки пути без ремонта в РСП. Старогодные рельсы и рельсовые плети, намечаемые для повторного использования в пути без проведения ремонта в РСП, ремонтируют в пути с выполнением следующих технологических операций (см. табл. 2.6):
- профильная шлифовка головки рельса;
- удаление наплывов металла на торцах в подголовочной части рельса с устройством фасок сечением 2×2 мм;
- уположение уклонов седловин в зонах болтовых и сварных стыков наплавкой, напылением металла и местной шлифовкой поверхности катания (дефекты 46.3; 47.1);
- удаление фасок на болтовых отверстиях в шейке рельса после ультразвукового контроля концов стыкуемых рельсов на отсутствие трещин;
- наплавка пробоксовин (дефект 14), выколов металла головки (дефект 17) и выкрошиваний наплавленного слоя (дефект 18);
- правка зоны болтовых и сварных стыков рельсоправильными машинами;
- уположение шлифовкой износов подошвы рельса в местах контакта с клеммами и костылями, кромок подошвы рельса в местах местных коррозийных повреждений (дефект 69) в пределах подкладок и прикрепления к рельсу заземляющих проводов.
Характеристики рельсов, отремонтированных с профильной обработкой головки в пути рельсошлифовальными поездами (РШП) приведены в табл. 2.8.

Требования к старогодным термоупрочненным рельсам, подлежащим профильной обработке головки (строжке и фрезеровке). Профильную строжку или фрезеровку головки старогодных рельсов производят со стороны бывшей нерабочей грани. Отремонтированные рельсы укладывают в путь с переменой канта — отфрезерованной или остроганной гранью внутрь колеи.
Для непрерывного фрезерования головок рельсов в отдельные штабели подбирают рельсы I, II и III групп годности, скомплектованные по высоте рельса с шагом 1 мм — для рельсов I группы годности, 2 мм — для рельсов II и III групп годности с расположением будущих рабочих граней головки в одну сторону. Ремонтный профиль головки рельса длиной 6 м и более формируется обработкой поверхности катания и боковой выкружки комплектом специальных фрез за один проход.
Ремонтный профиль головки после фрезерования имеет радиусы: 15 мм в зоне выкружки, 80 мм в переходной зоне и 500 мм в средней части; со стороны необработанной части головки — радиусы от 4 до 10 мм. Отклонения от проектного ремонтного профиля контролируют в трех точках: по его осевой линии, в зоне перехода от поверхности катания к выкружке и на боковом закруглении.
На последующую обработку строжкой и сварку отдельными партиями подаются комплекты рельсов длиной от 6 м и более, отнесенные к I, II и III фуппам годности, в зависимости от наработки по пропущенному тоннажу, размера и характера износа, наличия допускаемых повреждений.
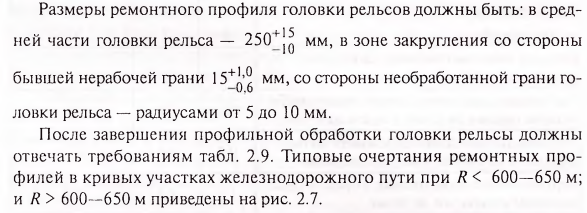
Маркировку старогодных отремонтированных сварных рельсов производят следующим образом. Сварные стыки отмечают масляной белой краской на расстоянии 100 мм с обеих сторон сварного шва полосами шириной 20 мм на шейке и верхней части подошвы. На одном из торцов рельса металлическими клеймами набивают маркировочные знаки, определяющие группу годности рельса; год сварки; номер, под которым рельс записан в шнуровую книгу; номер рельсосварочного предприятия.
Для термически упрочненных рельсов 1-А, 1, 1-А-П групп годности около цифрового номера сварного рельса дополнительно наносят букву Т.
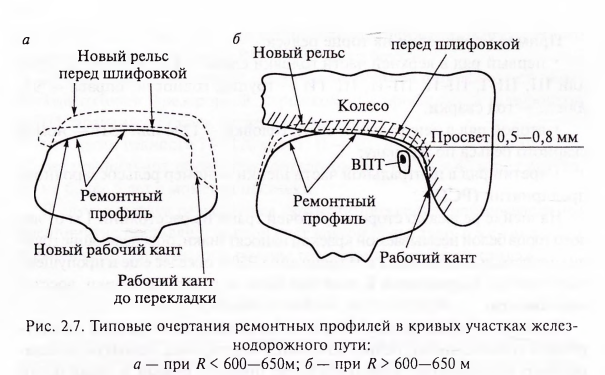
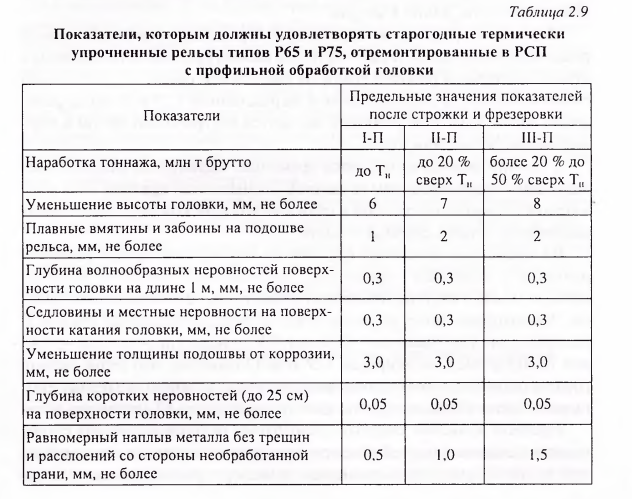
Пример маркировки на торце рельса:
- первый ряд в верхней части головки слева — 1-А, I, 1-АП, II, П-П или III, Ш-Т, Ш-П, Ш-И, Ш-ТИ — группы годности; справа — 95, или … — год сварки;
- второй ряд в центральной части головки — 1234 или 2519 — номер сварного рельса по журналу;
- третий ряд в центральной части шейки — номер рельсосварочного предприятия (РСП).
На шейке рельса со стороны рабочей грани на расстоянии 1 м от левого торца белой несмываемой краской наносят знаки, определяющие группу годности, а для рельсов I и II групп типа Р50 и тяжелее еще и пропущенный тоннаж. Маркировка Т, если она была на рельсе до сварки, восстанавливается.
В начале и конце рельсовой плети белой масляной краской на внутренней стороне шейки рельса наносится маркировка: номер рельсосварочного предприятия, номер плети по проекту, правая и левая плети рельсового пути, длина в метрах.
Маркировку рельсов звеньевого пути и рельсов, полученных резкой рельсовой плети, наносят светлой несмываемой краской на шейке рельса строго со стороны рабочей грани на расстоянии около 1,5 м от левого стыка или от места разрезки плети и на расстоянии 12,5 м от конца рельсовой плети. При этом работник находится внутри колеи лицом к маркируемому рельсу или плети.
В зимний период допускается временная маркировка мелом с последующим возобновлением ее светлой несмываемой краской. При маркировке старогодных рельсов в пути светлой краской восстанавливают маркировку старых сварных стыков.
На шейке рельса наносят следующую маркировку: группу годности рельса, вид и наличие упрочнения, пропущенный тоннаж (с округлением до 10 млн т брутто), номер дистанции пути, на которой сняты рельсы. Термоупрочненные по всему сечению рельсы маркируют буквой У, поверхностно упрочненные — буквами ПУ, нетермоупрочненные — буквой Н. Например, маркировка 1-У-680-12 означает, что рельс первой группы годности, термоупрочненный по всему сечению, по рельсу пропущено около 680 млн т брутто, снят рельс на путях 12 дистанции пути.
Гарантии качества сварных старогодных рельсов и сварных старогодных рельсовых плетей обеспечивает рельсосварочное предприятие при условии надлежащего хранения, транспортировки, укладки и эксп- 152 луатации пути. Срок гарантии установлен по количеству пропущенного тоннажа: для рельсов Р65 и Р75 — 120 млн т брутто.
Для повторно уложенных старогодных рельсов с профильной обработкой головки фрезеровкой, строжкой или профильной шлифовкой РШП гарантийный срок службы составляет:
для групп годности 1—120 млн т; II — 100 млн т; III — 75 млн т;
без профильной обработки соответственно 75, 50 и 40 млн т брутто, но не более 5 лет с момента поставки.